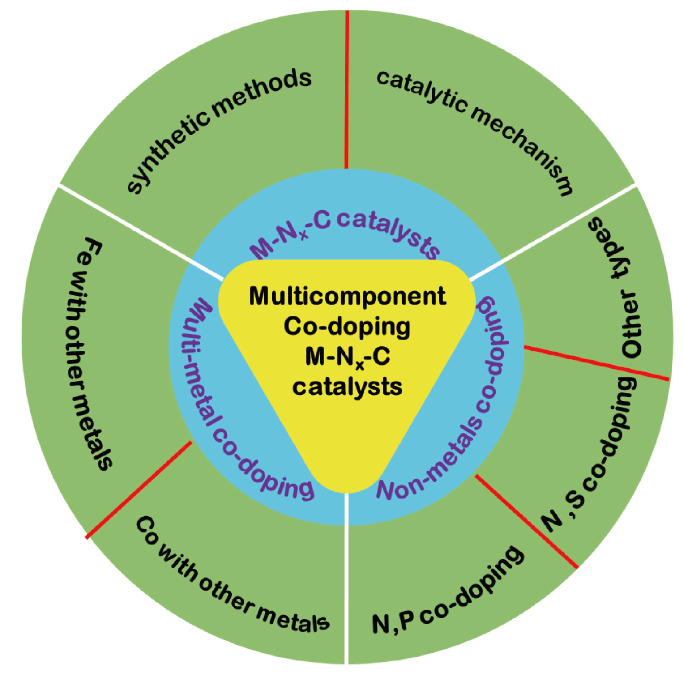
Contents
1 引言
2 M-Nx-C单原子催化剂
2.1 M-Nx-C单原子催化剂及制备方法
2.2 M-Nx-C单原子催化剂的催化原理
3 多种金属共掺杂的M-Nx-C单原子催化剂
3.1 铁与其他金属共掺杂
3.2 钴与其他金属共掺杂
4 非金属元素掺杂M-Nx-C单原子催化剂
4.1 N、S共掺杂
图8 (a) Fe-NSC的合成示意图;(b) 0.1 mol/L KOH 中的LSV 曲线(转速: 1600 r/min);插图为相应的半波电位和转移电子数[68]Fig. 8 (a) Schematic illustration of the synthesis of FeNSC. (b) ORR LSV curves for different catalysts in 0.1 mol/L KOH solution (rotation rate: 1600 r/min). Inset shows corresponding half-wave potentials and the number of transferred electrons[68] |
4.2 N、P共掺杂
4.3 其他多种非金属元素共掺杂
5 结论与展望
表1 近年M-Nx-C催化剂电化学性能汇总表Table 1 Summary of electrochemical performance of M-Nx-C electrocatalysts |
Catalysts type | structure | Carbon carrier | Acidic media | Alkaline media | ref | ||
---|---|---|---|---|---|---|---|
Eonesetvs RHE(V) | E1/2vs RHE(V) | Eonesetvs RHE(V) | E1/2vs RHE(V) | ||||
Non-doped M-Nx-C | Fe-N-C | histidine | - | - | 1.046 | 0.87 | 22 |
Fe-N-C | block co-polymer | - | - | 1.00 | 0.901 | 28 | |
Co-N-C | the mixture of polystyrene, polyacrylonitrile | - | - | 0.95 | 0.86 | 88 | |
Co-N-C | Zn/Co-ZIF | - | - | 0.982 | 0.881 | 30 | |
Cr-N-C | ZIF-8 | - | 0.773 | - | - | 32 | |
Cu-N-C | ZIF-8 | 0.83 | - | 0.99 | 0.895 | 36 | |
Fe-N-C | 2-MeIm | 0.963 | 0.835 | - | - | 38 | |
Fe-N-C | ZIF-8 | - | 0.78 | - | 0.864 | 34 | |
Mn-N-C | ZIF-8 | - | - | - | 0.90 | 35 | |
Non-metal elements doped M-Nx-C | Fe-N/S-C | UIO-66—NH2 | - | 0.785 | 0.97 | 0.87 | 67 |
Fe-N/S-C | formamide | - | 0.78 | 1.09 | 0.92 | 68 | |
Fe-N/S-C | porphyra | - | - | 0.96 | 0.84 | 72 | |
ZnCo-N/S-C | chitosan | - | - | 1.07 | 0.893 | 51 | |
FeN3P1 | - | 0.89 | 0.72 | 0.941 | 0.867 | 73 | |
FeN4P2 | - | 0.80 | 1.06 | 0.87 | 74 | ||
Co-N2P2 | - | - | - | - | 0.878 | 75 | |
FeCl1N4/CNS | - | - | - | - | 0.921 | 77 | |
Fe-N/S/P-C | ZIF-8 | - | 0.791 | - | 0.912 | 69 | |
Co-N/B-C | - | - | - | - | 0.83 | 79 | |
Mn-N/O-C | Mn-BTC | - | - | - | 0.86 | 70 | |
Multi-metal elements doped M-Nx-C | Fe/Ni-N-C | ZIF-8 | - | - | - | 0.02* | 56 |
Fe/Mn-N-C | ZIF-8 | - | - | - | 0.904 | 57 | |
Fe/Cu-N-C | PVP | - | - | 0.96 | 0.86 | 58 | |
Pt1-O2-Fe-N4 | - | 0.93 | 0.80 | - | - | 60 | |
FeNi-N-C | polydopamine | - | - | 0.95 | 0.82 | 87 | |
Fe/Co-N-C | ZIF-8 | - | - | 0.995 | 0.920 | 89 | |
Fe/Co-N-C | Co/Zn-ZIF | 1.02 | 0.86 | - | - | 61 | |
Zn/Co-N-C | Zn/Co-ZIF | - | 0.796 | - | - | 63 | |
Co/Ni-N-C | CoNi-NCNT | - | - | 0.88 | 0.81 | 64 | |
Co/Cu-N-C | DCDA | - | - | 0.98 | 0.88 | 65 | |
Fe/Ni-N-C | polystyrene spheres,ZIF-8 | - | 0.840 | - | 0.938 | 90 |
* negative than 20% Pt/C |